Anti-corrosion Protection
- Coating Protection: Apply coatings such as epoxy resin and polyethylene on the surface of the casing to isolate it from corrosive media.
- Corrosion Inhibitor Protection: Inject appropriate corrosion inhibitors into the well so that they can be adsorbed on the surface of the casing to form a protective film and inhibit the corrosion reaction.
- Cathodic Protection: Use the methods of impressed current or sacrificial anode to make the casing become the cathode and prevent the corrosion reaction on its surface.
Anti-wear Protection
- Use of Centralizers: Use centralizers when running the casing to keep it centered in the wellbore and reduce friction and collision with the well wall.
- Optimization of Drilling Technology: Reasonably select drilling parameters and optimize the performance of drilling fluid to reduce the impact of the drill bit on the casing and the friction between the casing and the well wall.
- Use of Wear-resistant Materials: Install wear-resistant shoes, use wear-resistant subsections and so on at the parts of the casing that are prone to wear, such as the bottom and near the wellhead.
Anti-deformation Protection
- Reasonable Design of Casing Strength: According to the geological conditions and production requirements of the oil well, and considering various factors, reasonably design the strength and wall thickness of the casing.
- Control of Cementing Quality: Ensure that the cement slurry is evenly filled in the annular space between the casing and the well wall, and that the set cement has sufficient strength and bonding performance, and control the cementing pressure.
- Avoidance of Abnormal External Forces: During the production and workover operations of the oil well, avoid applying excessive abnormal external forces such as tension, compression and bending to the casing.
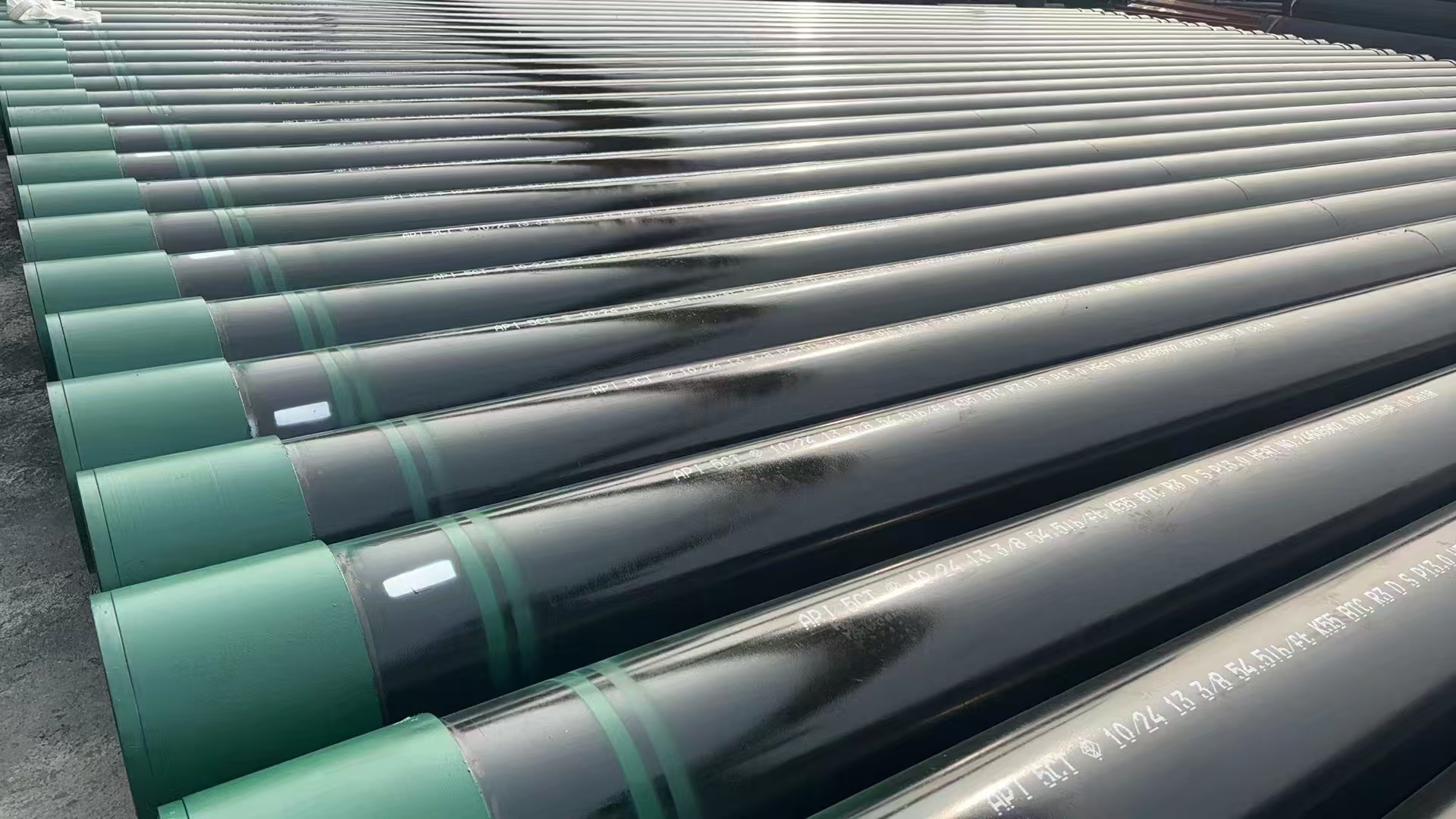